„Technische und wirtschaftliche Integration von CFK-Strukturen in den Werkzeugmaschinenbau“
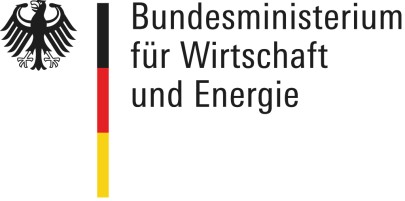
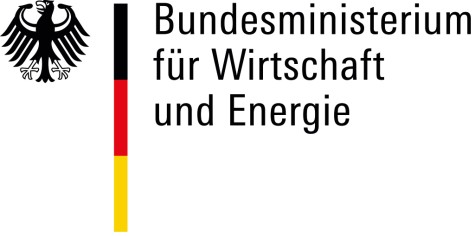
Das IGF-Vorhaben 409 ZN der Forschungsvereinigung VDW-Forschungsinstitut e.V. wurde über die AiF im Rahmen des Programms zur Förderung der Industriellen Gemeinschaftsforschung (IGF) vom Bundesministerium für Wirtschaft und Energie aufgrund eines Beschlusses des Deutschen Bundestages gefördert.
The manufacturers of machine tools are facing global competition, which is driven in particular by the build-up of corresponding capacities in Asian countries. In order to survive in this competition, constant improvements and innovations are necessary. To achieve high drive dynamics and increase feed rates, either the moving mass must be reduced or the driving power must be increased. The latter is not a target-oriented solution in view of the increasing importance of energy consumption and the higher acquisition costs. In contrast, lightweight construction can make a significant contribution and play a supporting role when it comes to increasing the speeds of the machines. However, the highest demands on machine accuracy or cost pressure must not be neglected under any circumstances.
The classic lightweight structural design with aluminium as the material, the use of sheet metal structures and topology-optimised casting can now be regarded as state of the art and is reaching its limits. The reasons given by machine tool manufacturers for the hesitant use and the lack of testing of alternative materials to date are the points of component strength, cooling lubricant compatibility, resistance to chip impact and, in particular, higher material and manufacturing costs.
Problem definition
The aim of this research project was to analyse and test how components made of CFRP can lead to an increase in performance through targeted optimisation of their dynamic and thermal behaviour.
Project goals
The increase in performance is to be investigated using two selected components from the machines of the project partners involved. For this purpose, both components will be constructed as CFRP demonstrators and tested in operation. The costs are to be kept low in comparison to conventional components through a material-appropriate design with semi-finished products, the avoidance of expensive manufacturing processes and the utilisation of secondary effects in comparison to previous fibre-plastic composite solutions. Long-term tests are being carried out to investigate the influence of cooling lubricants on CFRP components.