Machining with industrial robots
Duration: expired workgroup | 2017 – 2018
If you have any questions about this expired workgroup, please contact our institute management
oberingenieure@ptw.tu-…
The industrial working group “Machining with Industrial Robots” focuses on robot-based machining.
The following focal points are examined in relation to component quality:
- Compensation of industrial robot compliance
- Process parameters for machining
- Development of a method for the evaluation of industrial robots for machining
Objective
Industrial robots as processing machines offer many advantages over the use of cost-intensive machine tools due to the size of the workspace, flexibility and low investment costs. This is especially the case for large-volume components and complex geometries. However, they often do not meet the required accuracies in terms of path fidelity and absolute accuracy during the cutting process. This is partly the result of the low rigidity of the industrial robot, which leads to path displacement of the tool and low-frequency vibrations. Compensation methods that take the process forces into account have not yet reached sufficient industrial maturity.
Therefore, today's machining cells with industrial robots are designed and operated on the basis of empirical values. There is usually a lack of scientifically based recommendations for machining, for example with regard to the selection of suitable kinematics, the working space, the tools, the technology parameters as well as the compliance compensation.
Since 2003, PTW has been working on a large number of projects on the topic of “Machining with Industrial Robots”. These are, on the one hand, basic research-oriented, publicly funded projects of the German Research Foundation (DFG) and, on the other hand, application-oriented projects in close cooperation with the industry. The research focus of the working group “Machining with Industrial Robots” at the Institute PTW focuses on the industrial robot as a processing machine. This includes, among other things, the topics “process development and path planning”, “modelling of the robot structure and milling”, “tool validation” and “design and sensor integration”. The aim of the research is to increase the accuracy and quality of machined workpieces and to replace manual work that is hazardous to health and physically exhausting with robot-based processes.
Within the scope of the working group, a method, and also a software solution, for compliance compensation is being developed, on the basis of which, for example, robot manufacturers, calibration service providers or path planning specialists can offer user-friendly solutions for compliance compensation. The aim of the work packages is to create a compliance module, validated by tests, which compensates for deviations caused by external forces at the tool centre point (TCP) by recalculating the robot paths.
With regard to the goal of determining process parameters, correlations and effects of individual influencing factors on the machining process are being investigated and manufacturer-independent recommendations are being generated. In addition, activities in the field of standardisation of test procedures for the assessment of industrial robots for machining are targeted. Cluster II is the topic area “Process parameters for machining with industrial robots”.
Members

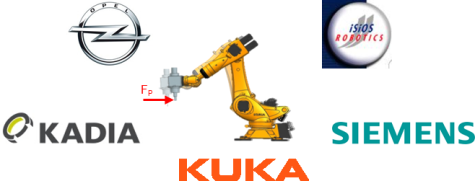