SIERPA | Simulation-based integration of the energy and resource consumption in the selection of alternative process chains in work preparation
Duration: Completed | 2012 – 2014
If you have any questions about this completed project please contact our institute management:
Oberingenieure@PTW.TU-Darmstadt.de
Rising prices for energy and raw materials increase the need for manufacturing companies to make their use in production as efficient as possible. The decisions made in work preparation determine the relevant energy and resource requirements in production at an early stage. Until now, there have been no methods to support production planning in the inclusion of energy and resource consumption in the selection process of alternative production sequences. Although various research projects dealt with the retrospective, ecological evaluation of process alternatives, a methodology for the prospective assessment and integration into production planning did not exist until now. Within the framework of the research project “EerFer”, the basics for decision support for energy- and resource-efficient production were worked out and calculation models of selected processes were developed. The approaches developed here enable an initial forecast of the energy consumption of alternative process chains. However, a methodical adaptation to the respective requirements and an optimisation and increase in accuracy of the previous models is necessary for use in a practical environment.
Within the framework of the “SIERPA” project, a method was accordingly developed that enables the production planner to prospectively determine the energy demand of different production machines. In this way, the energy demand in production can be considered as a further target variable in the selection of alternative production machines and process chains. The method takes into account in detail the four levels of consideration: Machine components, machine assemblies, machine and process chain.
Simulation models were implemented in Microsoft Excel and Visual Basic for Applications to estimate the energy demand at machine component, machine assembly and machine level. The linkage of different machines to a process chain was carried out within the material flow simulation environment Plant Simulation from Siemens PLM. As examples, machine tools, cleaning machines and hardening ovens were mapped as production machine types and linked to the model process chain from Bosch Rexroth. A key figure-based decision-making system was developed to integrate the simulated information on the energy requirements of individual production machines into the decision-making process of production planning. The decision-making system offers the possibility of combining different target variables in the selection of production equipment and deepens the newly introduced target variable of energy efficiency.
In summary, it can be stated that the research goal of enabling the production planner to estimate the electrical energy demand of production machines during the planning phase was achieved. All work packages described in the work programme were successfully completed.
Funding source
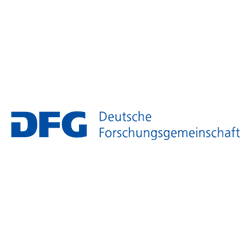